一、一體化壓鑄將成為新能源汽車的發(fā)展趨勢
一體化壓鑄的定義:一體化壓鑄是將汽車部件的鑄鋁化及集成化。其工藝特點是通過大噸位壓鑄機制造大型鋁制零部件,主要指汽車車身結構件一體化加工,將原本設計中多個單獨、分散的小件經(jīng)過重新設計高度集成,再利用壓鑄機進行一次成型壓鑄成完整零件(省略焊接及組裝流程)。此外,新能源車三電系統(tǒng)等多合一殼體也引入一體化壓鑄技術來實現(xiàn)集成制造。大型一體化壓鑄主要適用于乘用車下車身,包括后地板、前地板及前機艙、電池蓋以及白車身等。 新能源汽車帶來了一體化壓鑄市場的強勁需求,以特斯拉為引領,新勢力造車企業(yè)跟進,傳統(tǒng)汽車制造企業(yè)轉型,為未來的一體化壓鑄市場帶來了想像空間。 當前一體化壓鑄變革主要應用于新能源汽車車型開發(fā),其中造車新勢力功不可沒。特斯拉率先采用一體化技術,蔚來、小鵬、理想、小米、高合緊隨特斯拉布局一體化壓鑄。 傳統(tǒng)“沖壓+焊接”模式是傳統(tǒng)造車企業(yè)制造的主流,其切換速度仍比新能源車企業(yè)慢,做出樣件要耗時半年以上。2022年2月沃爾沃是第一家公告擬投資一體式壓鑄工藝的傳統(tǒng)車企。其后大眾汽車3月表示,已在德國沃爾夫斯堡-瓦爾梅瑙其主要工廠附近建立一個新生產(chǎn)基地,將引入一體化壓鑄工藝。國內(nèi)主流汽車廠一汽、長安、吉利、長城也在積極布局一體壓鑄,預計今年可完成樣件生產(chǎn)。
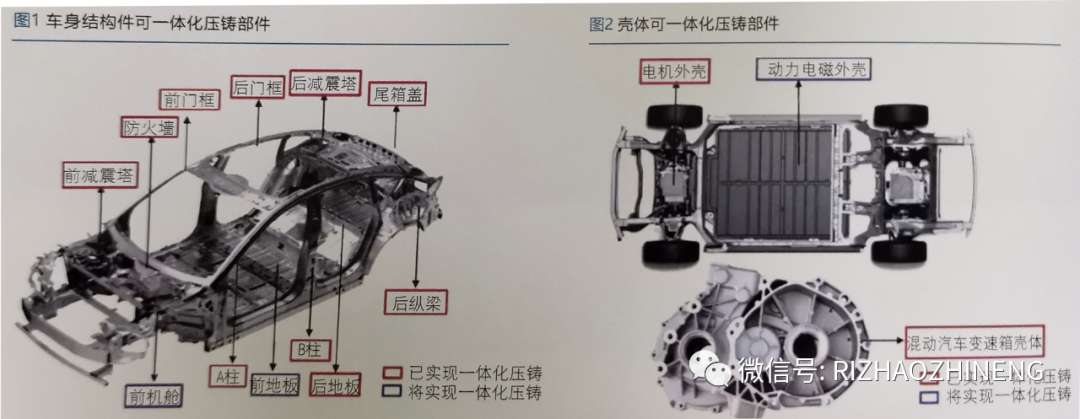
目前可以量產(chǎn)的一體化車身部件是特斯拉。其后地板率先量產(chǎn),前艙體緊隨其后,降本增效顯著。特斯拉是目前唯一實現(xiàn)后底板一體化壓鑄量產(chǎn)的主車廠。2020年9月22日,馬斯克在特斯拉電池日發(fā)布會上介紹稱Mode1 Y將采用一體式壓鑄后地板總成,鑄造零件可以從此前的70個簡化到2個,未來可能會合為1件。車身結構穩(wěn)定性和輕量化得到大幅優(yōu)化,同時還減少近1000次的焊接工序,節(jié)省約20%的生產(chǎn)成本。 后地板率先一體化壓鑄原因主要有以下幾方面,1)后地板碰撞受損的幾率小,安全性能要求相對其他下車體稍低;2)6000T大型壓鑄機可以滿足后地板制造條件,更大零部件設備正在研發(fā);3)一體化壓鑄后地板較傳統(tǒng)焊接工藝剛性更優(yōu),可更好兼顧底盤操縱性能。 國內(nèi)新勢力一體壓鑄布局中,蔚來汽車量產(chǎn)在即,小鵬汽車完成打樣,理想汽車完成打樣,小米汽車完成一體化壓鑄設備采購。 傳統(tǒng)汽車企業(yè)中的吉利汽車完成一體化壓鑄設備采購,長安汽車、一汽正在進行一體化壓鑄設備采購前的準備工作。 蔚來汽車布局一體化壓鑄。2021年10月18日,蔚來宣布成功驗證開發(fā)了可用于制造大型壓鑄件的免熱處理材料,全新材料將會應用在蔚來第二代平臺車型上,12月18日,蔚來在NIODay上發(fā)布,全新車型ET5的車身后地板相關部件將采用一體式鑄造成型,使車身后地板重量降低30%,同時后備箱空間增加11L。 小鵬汽車布局一體化壓鑄。武漢工廠加入了一體化壓鑄工藝車間,武漢工廠將引進二套(條)以上超大型壓鑄島及自動化生產(chǎn)線。1月18日,小鵬宣布與廣東鴻圖簽約12000噸超級智能壓鑄單元,以及新能源汽車 一體化前艙總成、一體化后地板總成和一體化電池托盤等關鍵和核心輕量化部件等項目。
輕量化及提效降本需求推動一體化壓鑄
減重:特斯拉計劃用2-3個大型壓鑄件替代原先370個零件組成的下車體總成,重量將降低30%。 降本:特斯拉后地板替換的成本下降在20%左右。實現(xiàn)下車身一體化后,制造成本下降40%。 提效:采用了一體式壓鑄后地板總成的Mode1 Y,用1-2件大型壓鑄件替換了原來的70個零件,焊點大約由700-800個減少到50個。制造時間由傳統(tǒng)工藝的1-2小時縮減至3-5分鐘,可實現(xiàn)在廠內(nèi)直接供貨。
二、產(chǎn)業(yè)鏈各環(huán)節(jié)空間與格局分析
隨著一體化壓鑄技術的成熟,前機艙、前地板、后地板、上車身結構件均實現(xiàn)一體化壓鑄,需要2臺6000t、1臺9000t、1臺12000t壓機,單車價值量12200元;2)全球乘用車銷量達到10000萬輛,中國乘用車銷量達3000萬輛,一體化壓鑄滲透率50%;3)壓鑄機規(guī)劃產(chǎn)能10萬套/臺,產(chǎn)能利用率70%,良率90%,設備更換周期10年,6000、9000、12000t壓鑄單元價格分別為5000、7500、10000萬元;4)免熱處理鋁合金單價18元/kg;5)模具一年更換一次,6000t、9000t、12000t壓鑄機對應模具單價分別為500、600、700萬元。
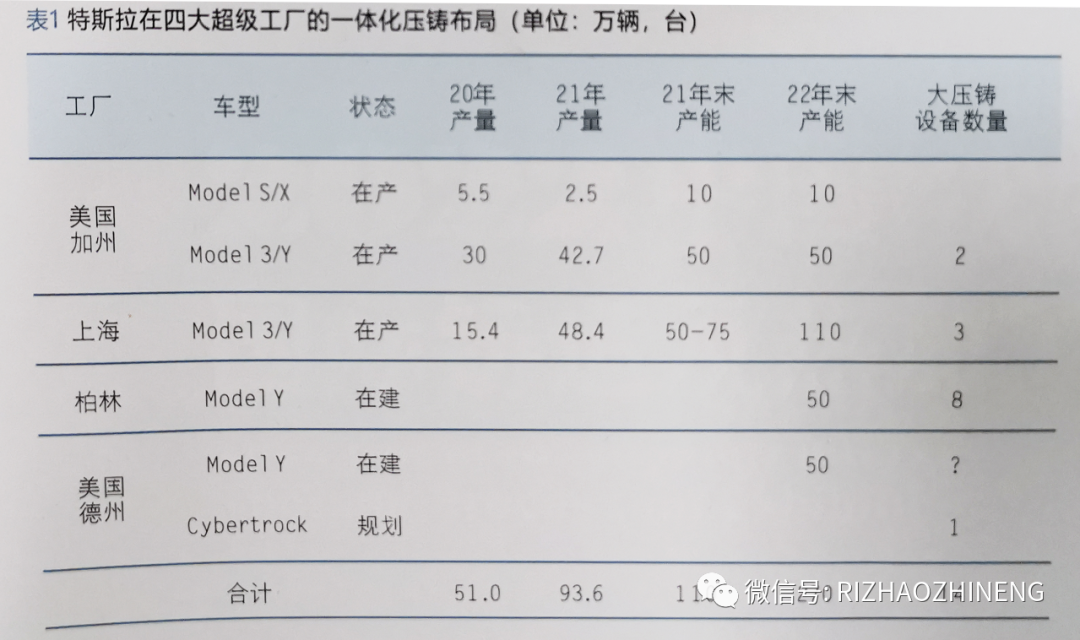
預計到2025年,一體化壓鑄車身結構件市場空間分別有望達到376.7億元,復合增長率160%;大型壓鑄機市場空間分別有望達到50億元,復合增長率90%;免熱處理鋁合金材料市場空間有望達到161.3億元,復合增長率139%;模具市場空間有望達到10.9億元,復合增長率131%。產(chǎn)業(yè)鏈各環(huán)節(jié)均有翻倍及以上的增速,其中一體化壓鑄車身結構件增速最快。 單車價值量按1)前機艙2200元、前地板3500元、后地板2000元;2)2023年前機艙實現(xiàn)量產(chǎn),2024年中地板實現(xiàn)量產(chǎn)。 未業(yè),一體化壓鑄車身結構件市場全球及中國市場空間分別有望達到6100和1830億元;大型壓鑄單元全球及中國市場空間分別有望達到218.3和65.5億元;免熱處理鋁合金材料全球及中國市場空間有望達到2500和750億元;模具全球及中國市場空間有望達到182.5和54.8億元。
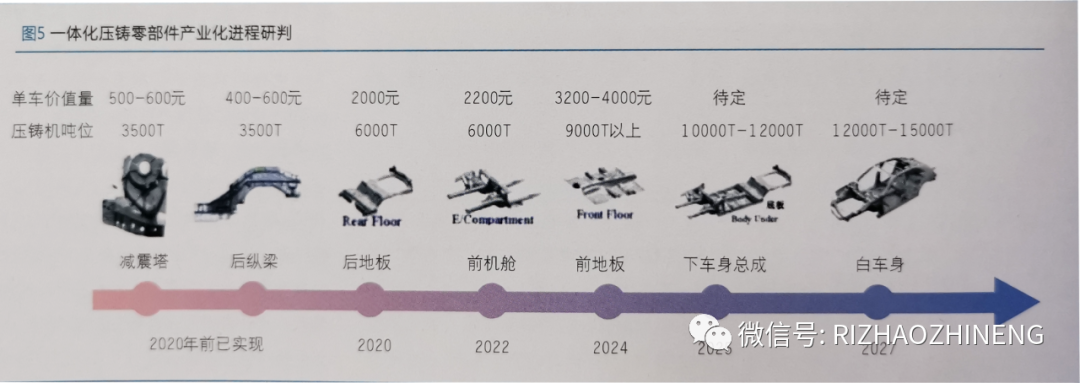
大噸位壓鑄機格局分析
大型壓鑄機主要玩家有老牌瑞士廠商布勒、國內(nèi)上市公司龍頭力勁科技、伊之密,以及海天集團子公司海天金屬等。瑞士布勒、中國力勁以及海天是目前具備規(guī)模量產(chǎn)6000噸以上大型壓鑄機的制造商。

力勁科技及子公司意德拉率先量產(chǎn)6000t壓鑄機并供貨特斯拉。根據(jù)意德拉官網(wǎng)產(chǎn)品介紹,在合模力、壓射力、模板 尺寸、射料量上均有明顯突破。2021年力勁發(fā)布9000噸大型壓鑄機,將壓鑄機的噸位再向前推進一步。12000t壓機正在與廣東鴻圖等公司合作研發(fā)。布勒在21年初發(fā)布6100t壓鑄機,預計在2022年發(fā)布9000t壓鑄機;海天金屬8800t壓鑄機也已完工交付美利信。
一體化壓鑄鋁合金材料格局分析
國內(nèi)一體化壓鑄鋁合金材料格局是國外技術領先,國內(nèi)迅速跟進。 1985年,在德國漢諾威展會上,兩名身材苗條的女子毫不費力地舉起了奧迪100的全鋁車身,推開了車身輕量化的第一道任意門。在此之前,鋁合金主要是用在航空領域,它的成分一度被德國視為國家機密,之后才慢慢走入了汽車領域。相比于傳統(tǒng)的低碳鐵,鋁合金要輕三分之一,伸縮性和可塑性更好,能夠在發(fā)生碰撞的時候更好地吸收潰縮(即通過變形分散碰撞動能)。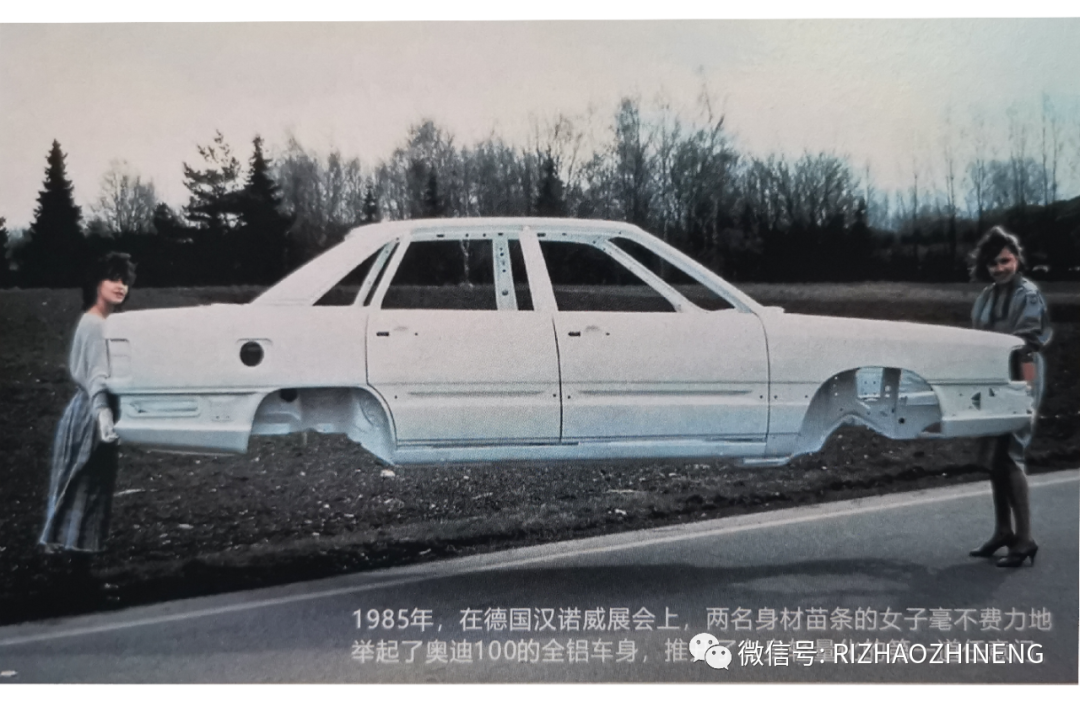
然而,一種新材料想要被量產(chǎn)車所接納,只是性能出色還不夠,換了新的材料就需要新的工藝或者結構,只有三者配合默契才能實現(xiàn)“質(zhì)量-成本-性能”之間的平衡。 對于傳統(tǒng)鋁合金而言,熱處理是保障壓鑄零部件機械性能的必備手段,熱處理過程易引起汽車零部件尺寸變形及表面缺陷,由于一體化壓鑄零部件較大,因此后期再進行熱處理將產(chǎn)生較大程度變形,因此需要使用免熱處理鋁合金材料。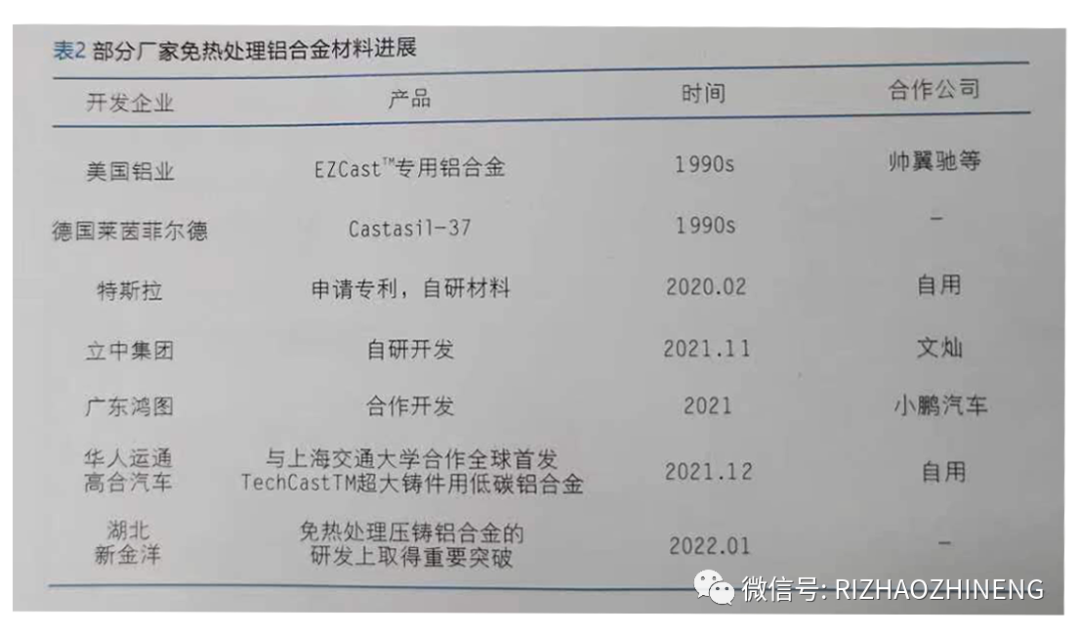
免熱處理鋁合金國外有美國鋁業(yè)、德國萊茵公司,國內(nèi)有立中集團、帥翼馳、上海交大等,具體見上表。
一體壓鑄模具格局分析
國內(nèi)一體壓鑄模具目前主流趨勢是主機廠與供應商合作共進。 目前一體化壓鑄車身結構件模具進展較快的主要有:廣州型腔、寧波臻至以及寧波賽維達。其中廣東型腔已經(jīng)為美利信配套8800t超大型壓鑄機一體化后地板壓鑄模具,與鴻圖、力勁以及廣東鴻勁簽署了《12000噸超級智能壓鑄單元聯(lián)合研發(fā)合作協(xié)議》,共同就12000T(噸)超級智能壓鑄單元開發(fā)項目開展合作。寧波臻至模具為寧波海威開發(fā)了前艙體一體壓鑄模具。寧波賽維達為特斯拉、拓普開發(fā)了車身一體壓鑄模具。
國內(nèi)一體壓鑄企業(yè)未來格局分析
國內(nèi)一體壓鑄企業(yè)初期格局將以整車廠自制和外部壓鑄企業(yè)供應并存。
特斯拉率先采用一體化技術,蔚來、小鵬、理想緊隨特斯拉布局一體化壓鑄,傳統(tǒng)主機廠中如吉利、大眾、沃爾沃、比亞迪、長安等也有相關入場計劃。特斯拉后地板、前艙體已經(jīng)實現(xiàn)量產(chǎn)自制,小鵬汽車以自制與外部壓鑄企業(yè)供應同時進行。理想和蔚來或主要依托外部零部件廠商。預計中期格局會因重資產(chǎn)低周轉屬性導致外部一級供應壓鑄企業(yè)主導更占優(yōu)。 長期來看,一體化壓鑄屬于重資產(chǎn)的領域,壓鑄單元單條生產(chǎn)線投資近一億元,而年產(chǎn)能只有6-8w套。據(jù)測算,在良率達到90%時,投入產(chǎn)出比仍高達1:2;毛利率在37%左右。而主機廠的固定資產(chǎn)周轉率較高,廣汽和長城等主機廠長期保持在3以上,可以看出其經(jīng)營特點并非重資產(chǎn)。因此,短期主機廠尤其是特斯拉和小鵬等新勢力出于保供壓力以及外部一級供應壓鑄企業(yè)能力未普遍成熟時期親自涉足,但是長期看一體化壓鑄資產(chǎn)較重,后期在產(chǎn)能充足以及工藝逐步成熟后將由外部壓鑄企業(yè)主導。